HANUMAN ICONIC J CLASS YACHT ARRIVES AT HOLTERMAN SHIPYARD FOR REFIT
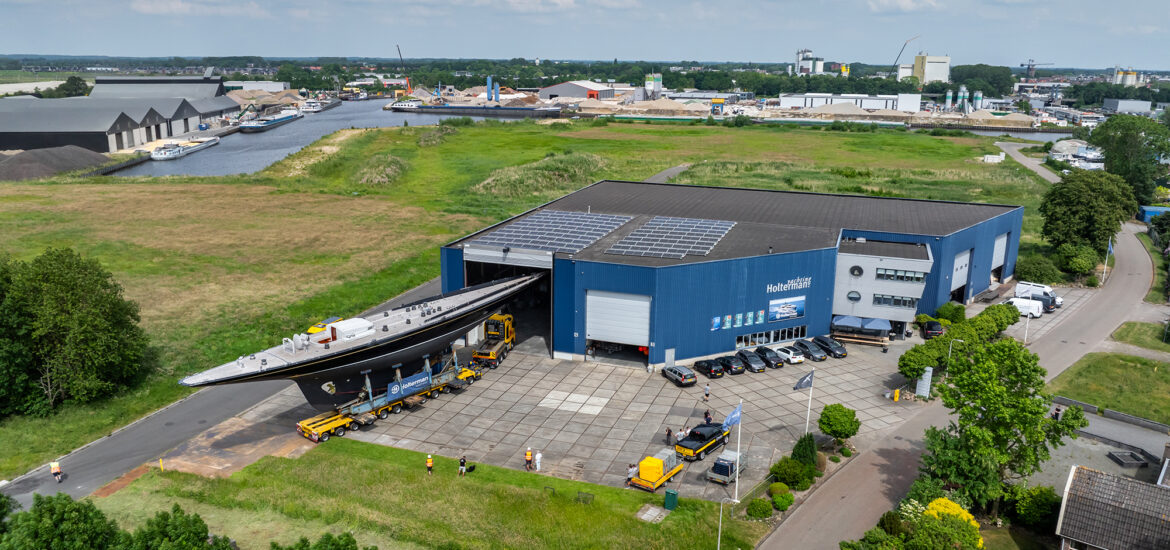
While the latest foiling America’s Cup yachts may be at the forefront of sailing technology, it’s a fleet of Cup racers from a bygone era that evoke passion and stir the senses and emotions among sailors and the public alike. The J Class yachts have become icons not only of a stunning aesthetic, but also of the pinnacle of modern big-boat racing as a growing fleet of Js, all built to the class rule and all following original designs, battle it out on one of the most spectacular race circuits on the planet.
The prestige of the Js is matched only by the incredible level of responsibility involved their care and maintenance – a responsibility that Holterman Shipyard in the Netherlands has proven perfect to take on with the arrival of Hanuman JK6 for an extensive refit. Based on a 1937 design by Charles Nicholson, Hanuman was launched in 2009 and has been a staple of the J Class racing scene where she scored overall victories in events such as the St Barths Bucket and the Superyacht Cup Palma.
That the owner, owner’s representative and crew agreed on Holterman to undertake the refit of Hanuman speaks volumes to the capabilities of this unassuming shipyard based in Meppel. “Although the shipyard mainly does new-build motoryachts, it has completed refit works in the past, including not only its own models but also, for example, a 30-metre motoryacht,” says Tim Wedzinga, Refit Manager at Holterman Shipyard. “Refit is an area we are really looking to expand, as what we can offer is second to none – and having Hanuman, an iconic J Class sailing yacht, arrive for extensive works shows just what we can do.”
Hanuman arrived in the Netherlands at the end of April, and after the rig was stepped and the yacht was carefully loaded onto a transport barge, she arrived at Holterman’s Meppel yard at the end of May for the full programme of works to begin in earnest. “The idea of the refit started with the need to replace the teak decks, but that has expanded to include something in every area of the yacht,” Wedzinga explains. “We will be installing a whole new air-conditioning system, new fridge freezer systems, upgrading the hydraulic system, replacing some interior floor soles, moving some deck hardware to more optimal positions, varnishing wood elements, and painting the underwater body and the topsides.”
The success of the refit will be strengthened by two key factors. First is the inhouse knowledge that is directly relevant to the project, as Wedzinga and several other members of the Holterman team have direct experience of Hanuman either from racing on her as crew or through their involvement with the original engineering of the yacht and its construction.
Second is the low-overhead, minimal management structure and the straightforward approach to such an involved project that the Holterman team can take. “It’s essentially a year’s worth of refit that we need to finish in seven months because the yacht needs to be ready for the 2025 St Barths Bucket,” Wedzinga quips. “But we’re pretty low-key here – we don’t have a management-heavy structure, we don’t need to have 10 meetings a day, there’s just a good bunch of people from our skilled inhouse carpenters to our key subcontractors that makes us the perfect choice for a no-nonsense, top-quality refit, even on a tight schedule!”
With the shipyard making a couple of minor alterations to its sheds to accommodate the 42.19-metre yacht, works have already begun on the first stage of the refit which includes unmounting the rudder, removing 500 pieces of deck hardware, and stripping the old deck down to the bare aluminium.
“I think the Hanuman project will surprise a lot of people because it’s not what Holterman is known for, but I think it really shows our flexibility,” Wedzinga concludes. “We never say no, and we will always find solutions to accommodate a project. And Hanuman will really stand as an example of the skills we have not only within Holterman in terms of craftspeople, but also in terms of coordinating a complex project with minimal fuss while ensuring maximum quality.”